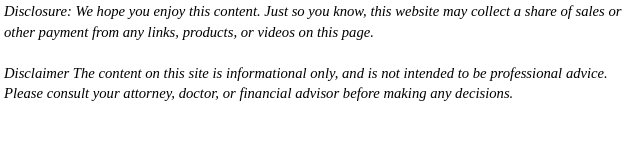
The introduction of the first hot runner systems ushered in the need for valve gate hot runner nozzles into the injection molding industry. It is a technology that is widely used as it offers more process flexibility something that cannot be achieved by the thermal gate systems. By using valve gating with molding machine nozzles, there are various techniques that we can engage in such as eliminating the drool and gate string, improving physical properties with lower mold stress, cycling the time reduction, balancing molds, and using superior molding processes for thinwall parts.
Typical valve gate systems are controlled by either pneumatic or hydraulic cylinder mechanisms connected to hot runner nozzle pins, which then open and close the gate area controlling the injection molded part filling and packaging.
Valve gate systems ensure optimum performance of cosmetic gate and also stop the drooling of molten plastic during vertical injection molding, although the vast majority of hot runner systems sold are still operational thermally with all of the advantages of their use.
Now that we understand a bit about molding machine nozzles and injection molding, let’s take a look at how important these processes are to many businesses today.
The Importance of Molding Machine Nozzles and Other Equipment Necessary in Plastics Manufacturing
Today, nearly one million Americans have some type of career in plastics manufacturing due to the growing interest in plastics. The United States is actually known for being the world’s third-largest plastic producer, with a huge need for these types of products to make things that we use on a daily basis.
However, many other parts of the world depend on these products as well. In fact, China is known for being the largest producer of plastics. They contribute 25% of the world’s plastic production, making them a worldwide provider. With us competing with many other countries in producing plastics, it is no surprise that we continue to better our output of plastic products.
The right equipment helps us continue to put out plastic products like never before. As we continue to product plastics and more consumers buy them for personal use, our role in the world of plastics continues to increase and bring in money every year.