
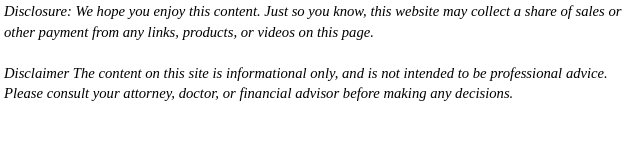

CT scanning technologies have come a long way since they were first introduced in the 1970s. Improved CT scan technology and speed combined with digital imaging have led to many new applications across a wide range of industries, including but not limited to aerospace, automotive, engineering products, forensics, geology, energy and electricity, medicine, archeology and defense. For OEMs, non destructive testing of parts and laser inspection equipment can save both time and money in carrying out inspections of industrial parts.
How do CT scans work?
Computerized tomography (CT), also known as computerized axial tomography’ (CAT) scans data from multiple X-ray images to create a computerized image of the structures inside a solid object like a human body, an archeological artifact or an industrial part. Tomography is a way of creating a 2D image of a 3D object.
When CT scans were first introduced in the world of medicine in 1974 and 1976, they were slow and cumbersome. They were originally used only for head imaging, but by 1976, whole body imaging was made possible. By 1980, CT scans were more common, and now there are around 30,000 around the world and about 6,000 in the U.S.
New applications for 3D imaging
3D scanning technology has progressed far beyond the early years when it was slow and its use was limited to medical purposes. With vastly improved speeds and accuracy, many new and innovative applications are being found for 3D scanning. New technologies like laser inspection equipment and X-ray inspection have many advantages over old methods of testing industrial parts.
Some of the uses of CT scanning in inspection are:
- Preproduction inspection
- Production inspection
- Lots inspection of suspect parts
- Overcapacity inspection for companies that have CT systems in house
- Failure inspection
At all stages of the production process, from pre-production to failure testing, CT scans can save both time and money for parts manufacturers. For example, using industrial CT scanning for new product inspection and failure analysis can reduce the costs by 25 and 75% respectively as compared to existing inspection methods.
X-ray inspection services for industrial parts
Using a variety of CT scan systems, parts inspection can be thorough and accurate. Parts as small a 5mm long to large ones that are 660mm in diameter and 1m long can be scanned. Laser inspection equipment and CT scanning equipment are typically not sold to manufacturers, but parts inspections services are offered. This is because the inspections can be done by thd specialist company most efficiently in-house, since they have a variety of CT systems to produce a complete scan.
Where industrial parts inspection would have taken weeks and required the destruction of the parts to be tested, non destructive testing using CT scans and laser inspection equipment can be done in a few hours, with results that are both instantaneous and accurate. It enables manufacturers to reduce costs and save time, while improving the quality of their products.